
MyRCCar 1/10 MTC Chassis Updated. Customizable chassis for Monster Truck, Crawler or Scale RC Car
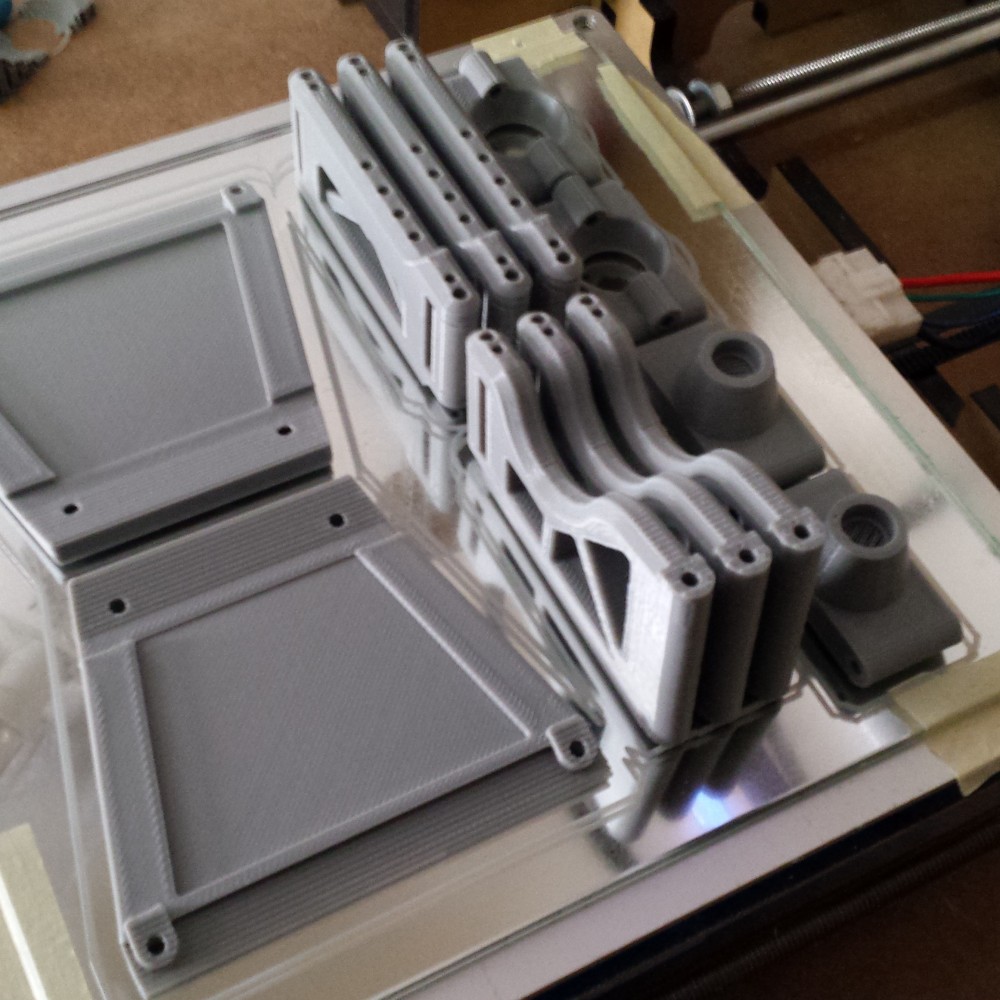
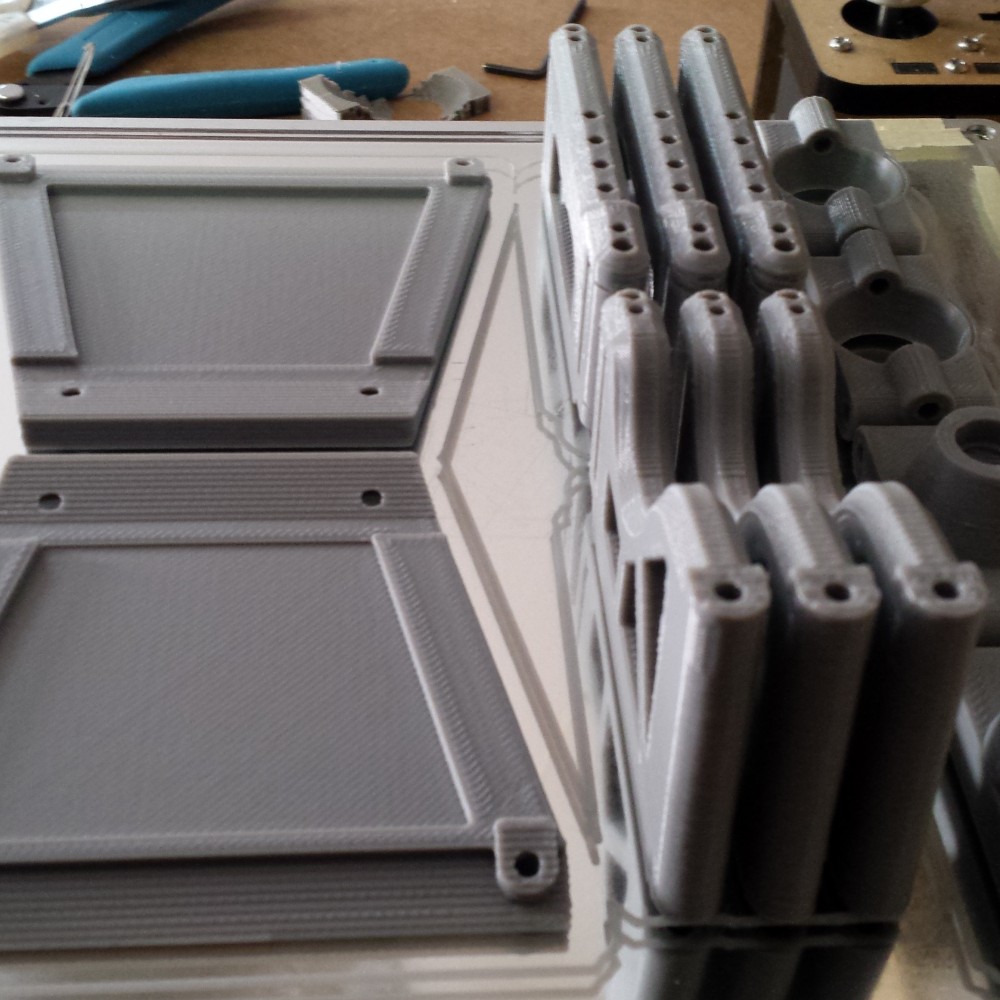
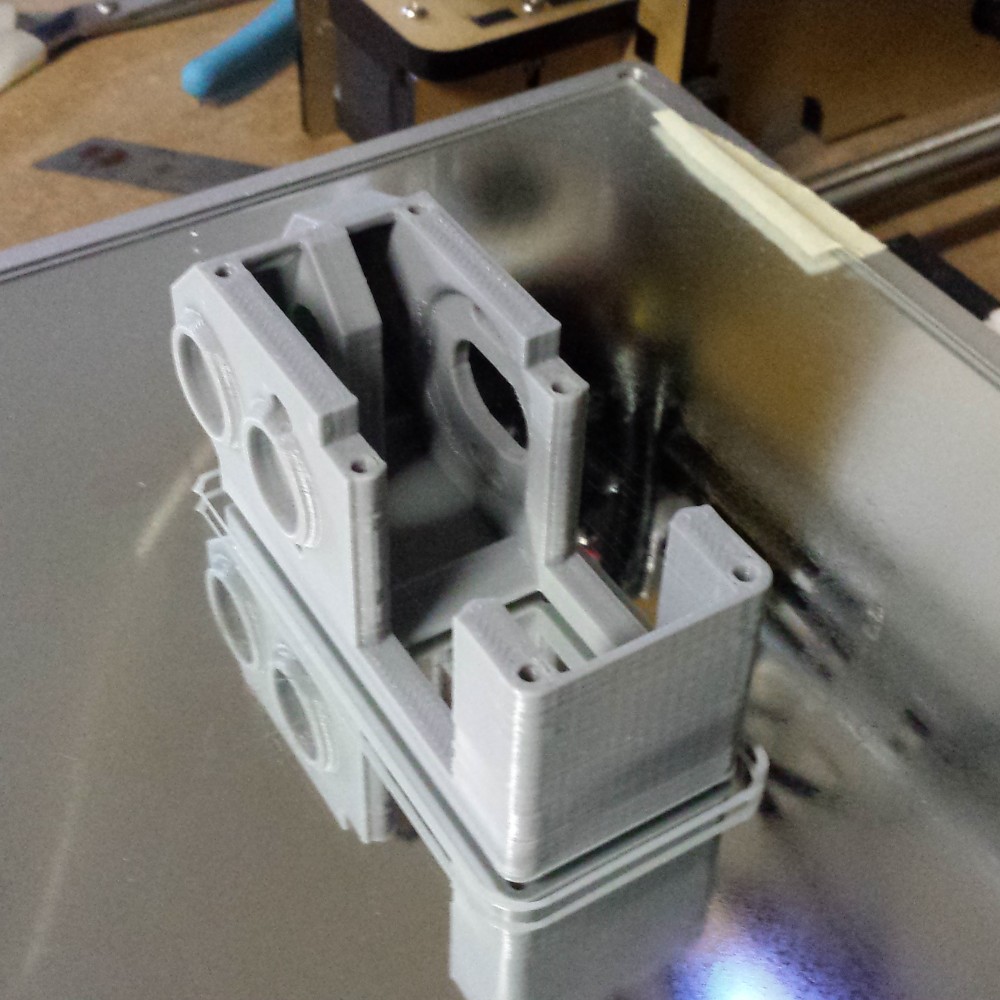
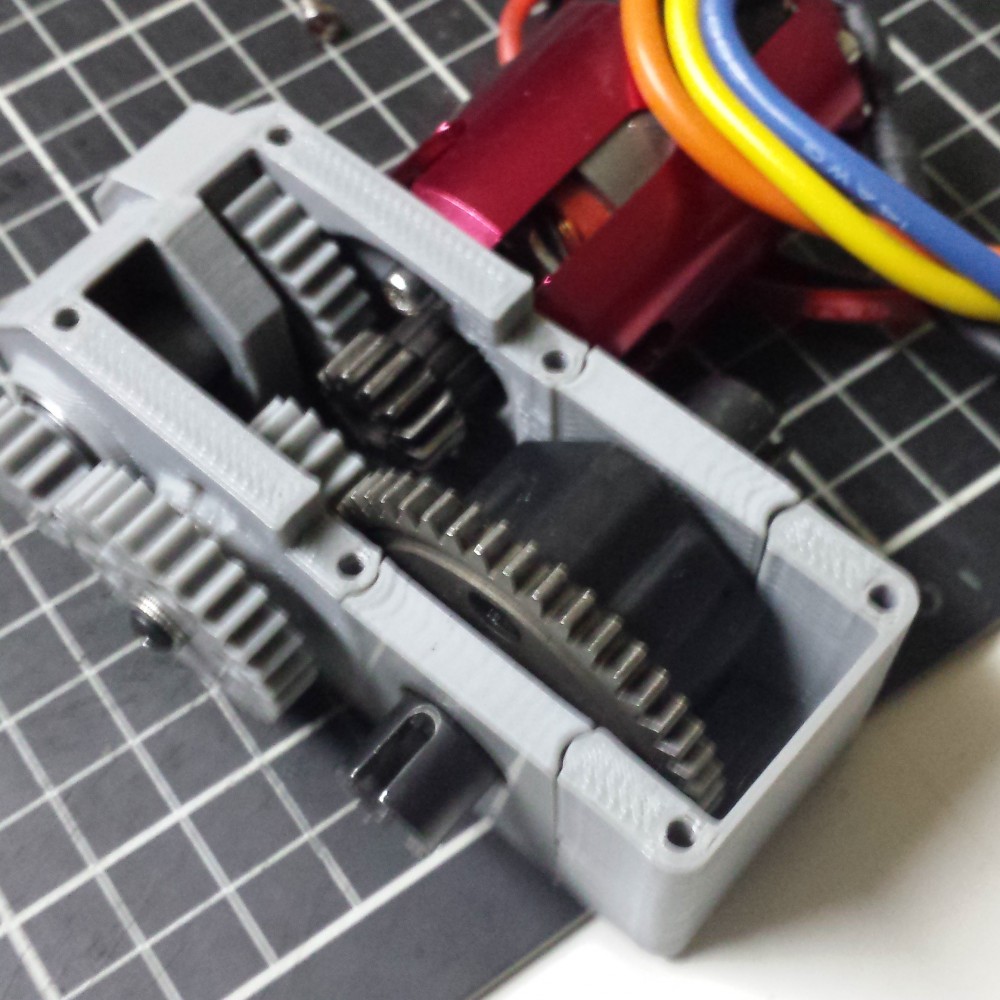
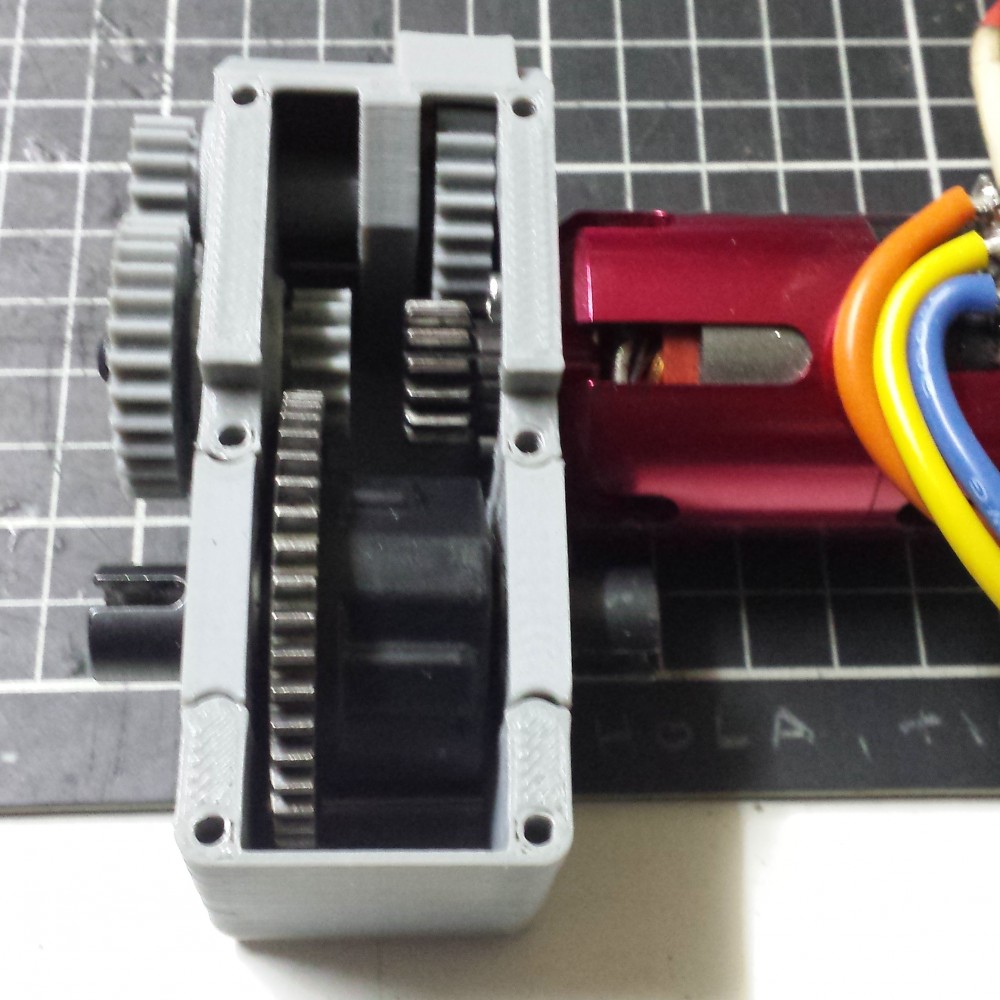
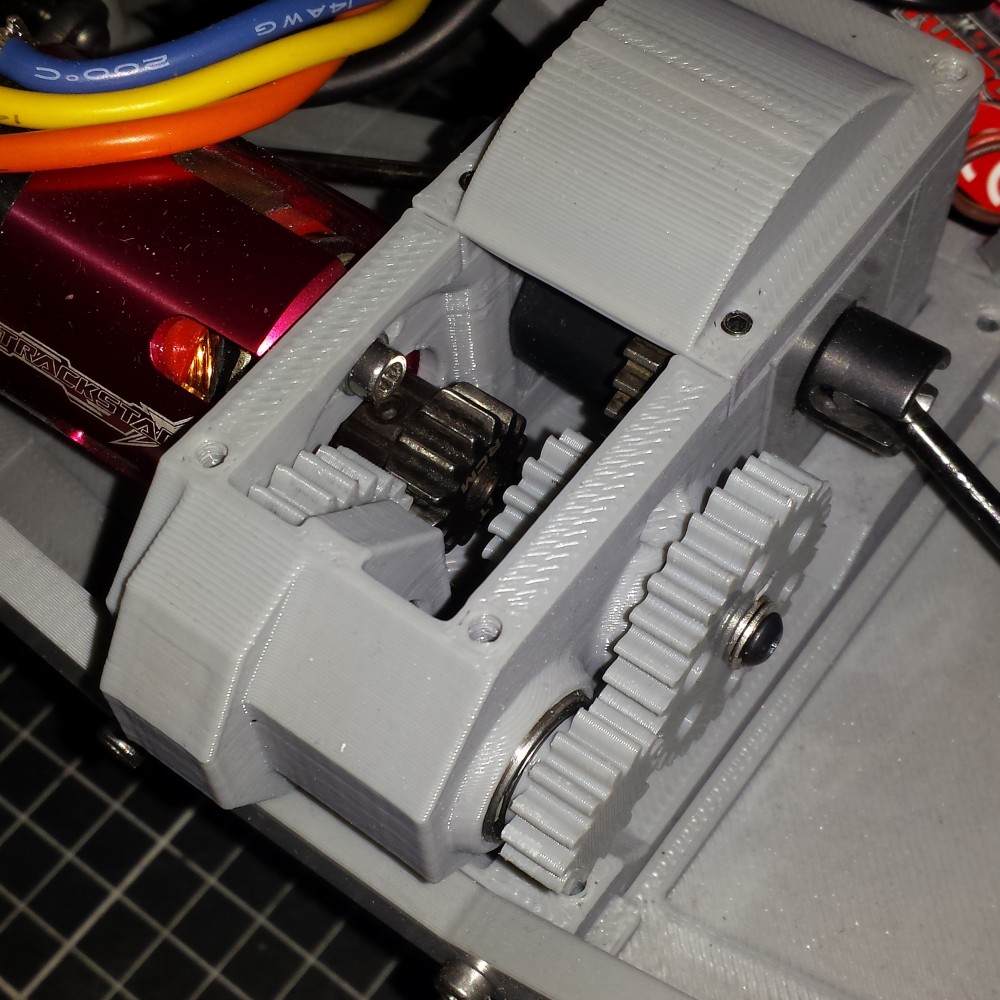
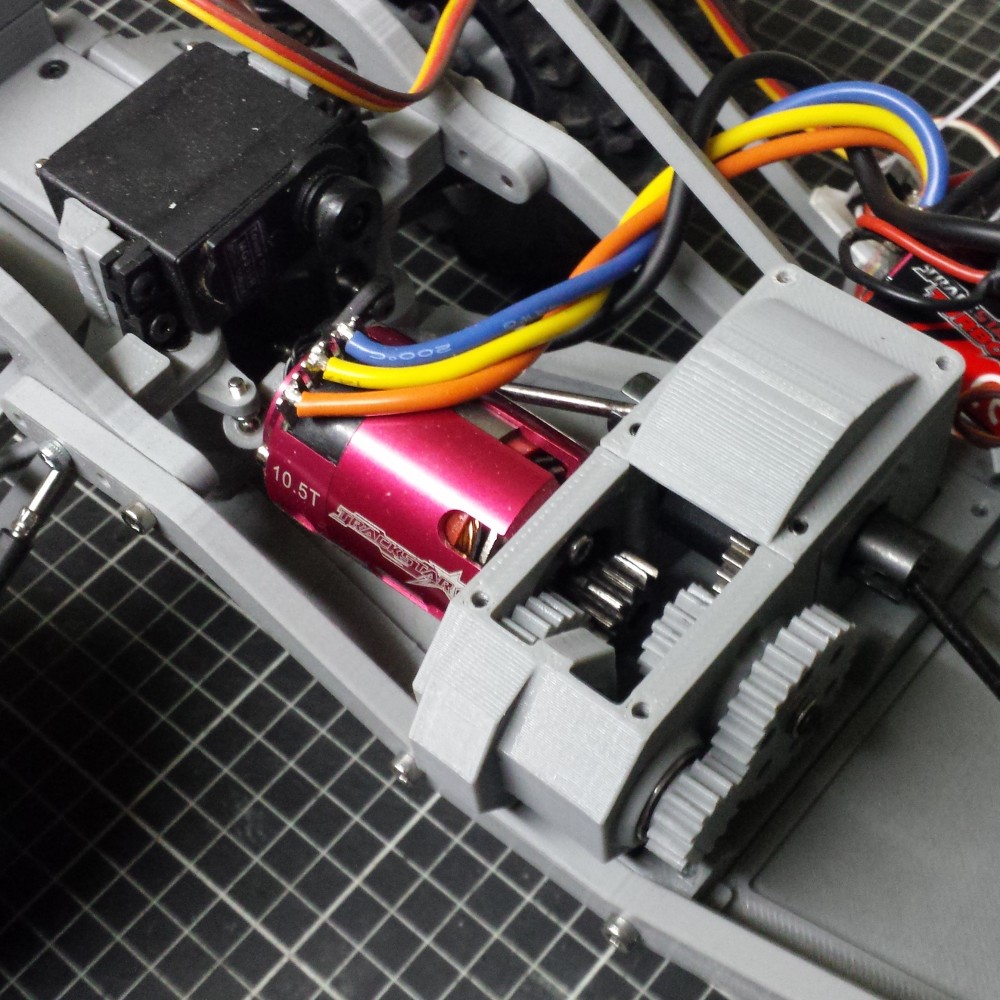
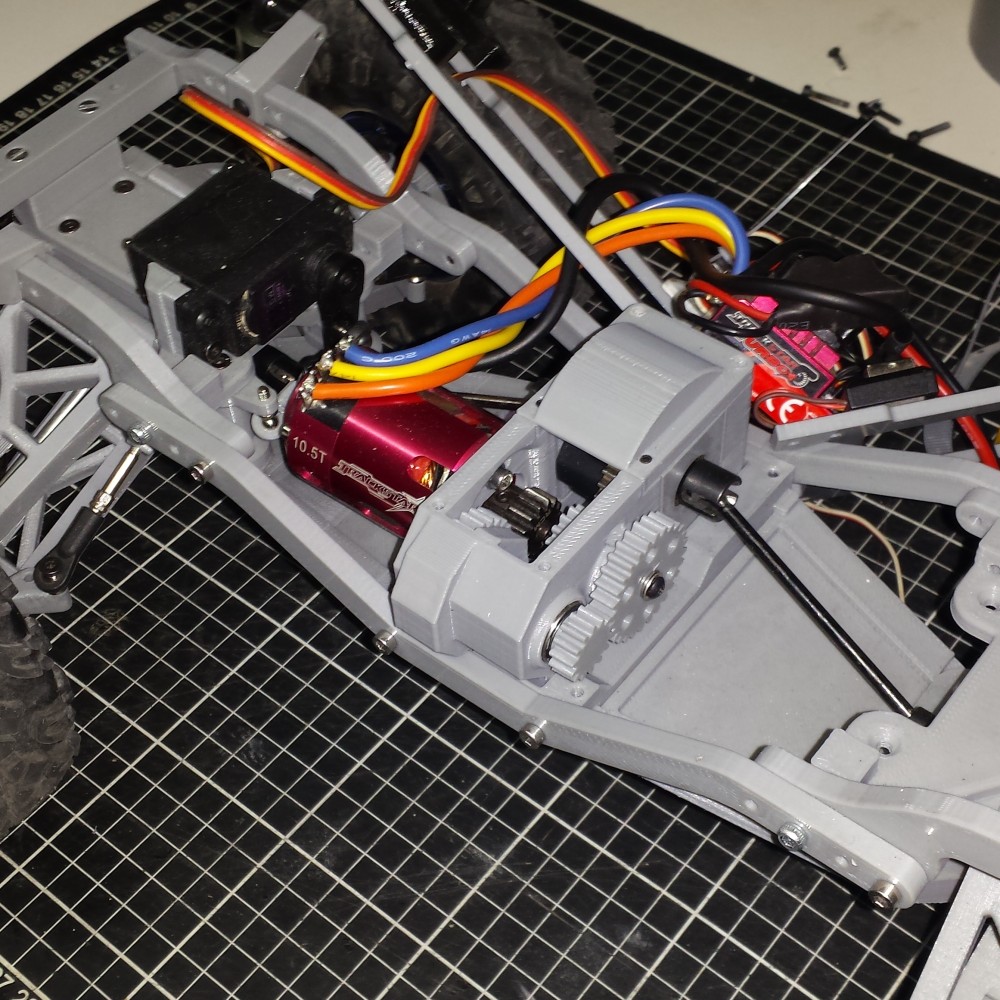
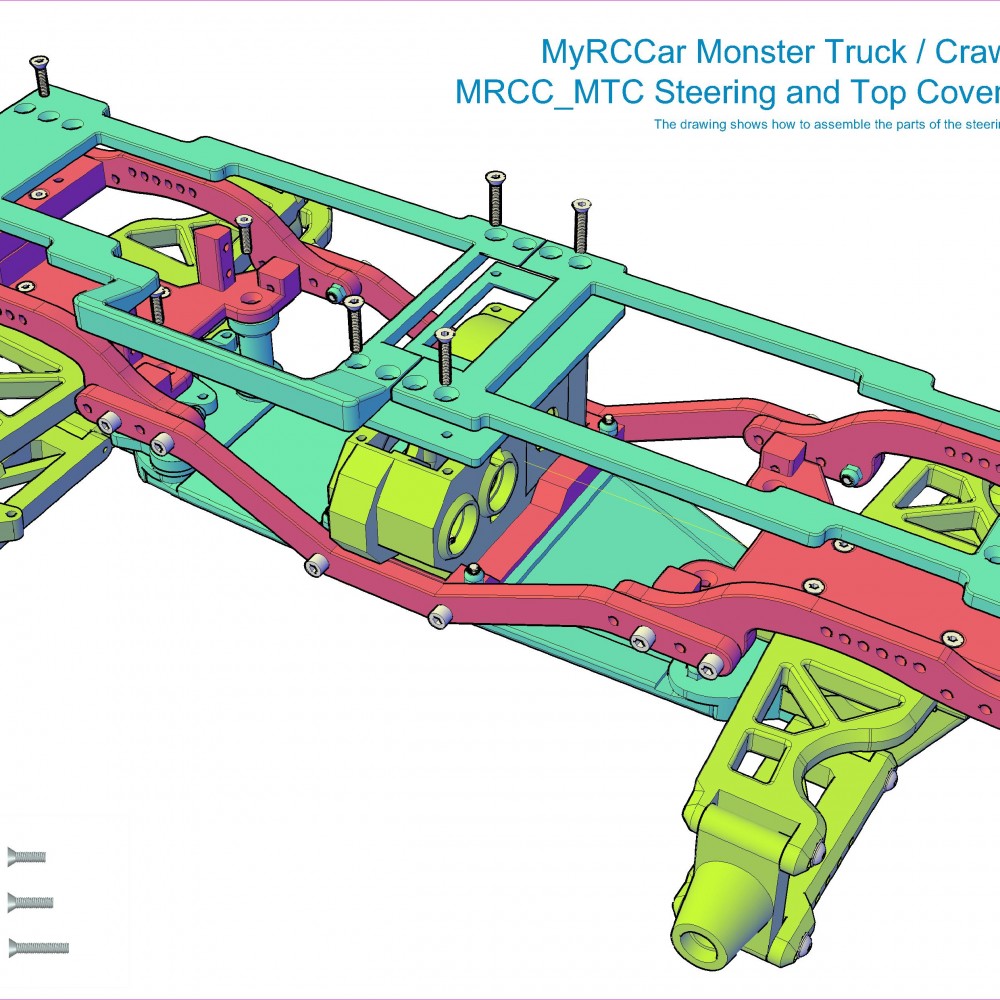
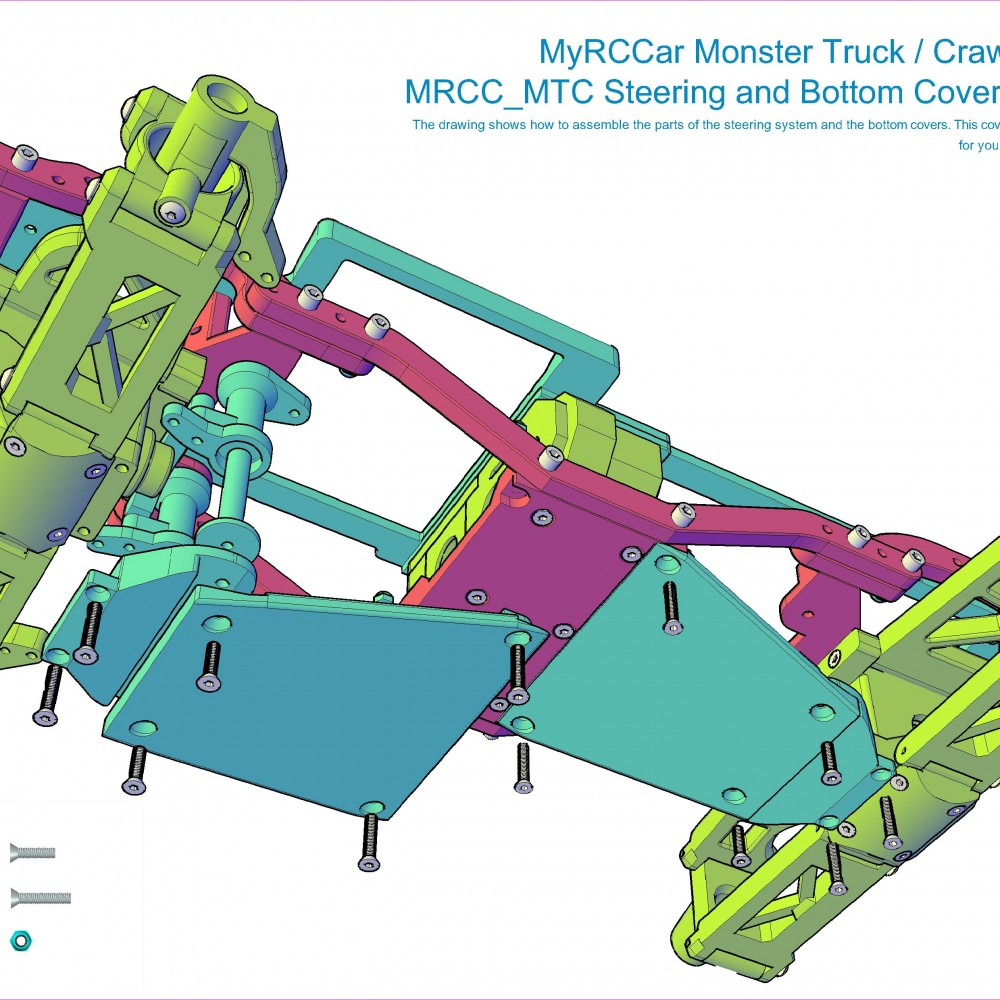
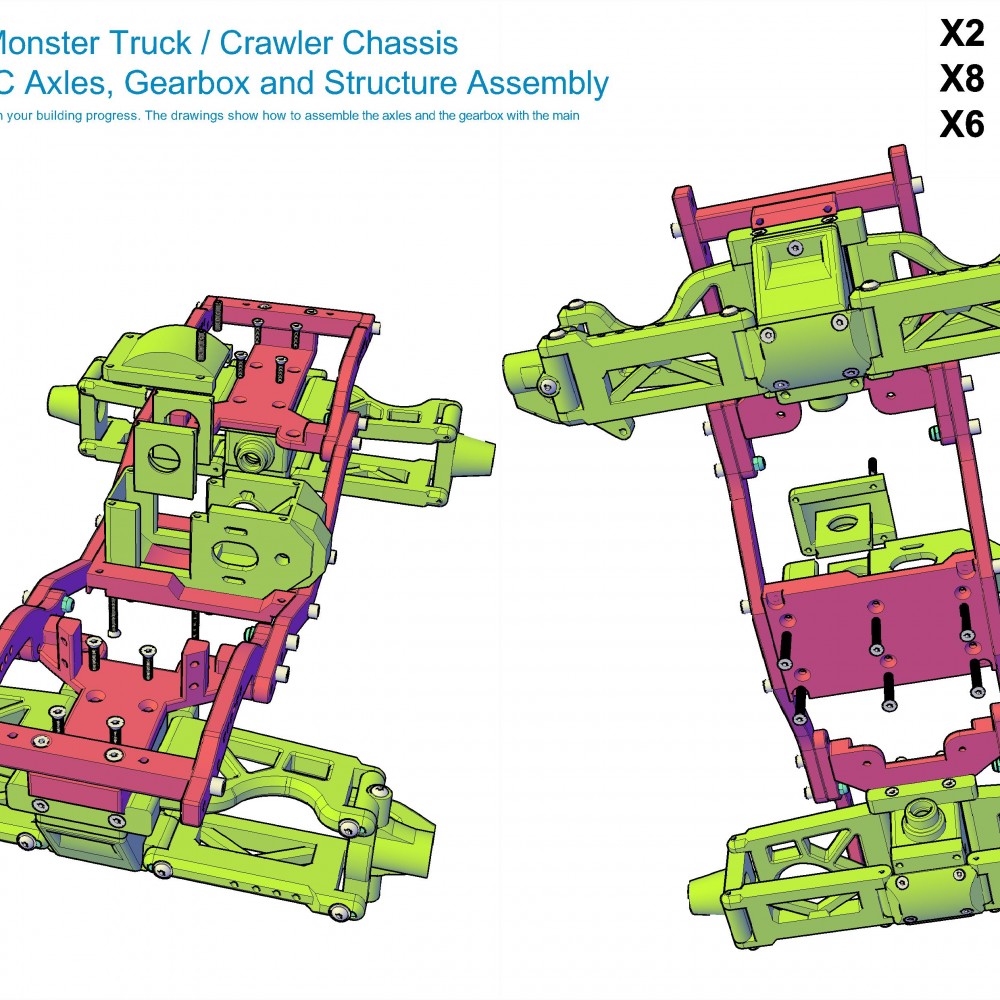
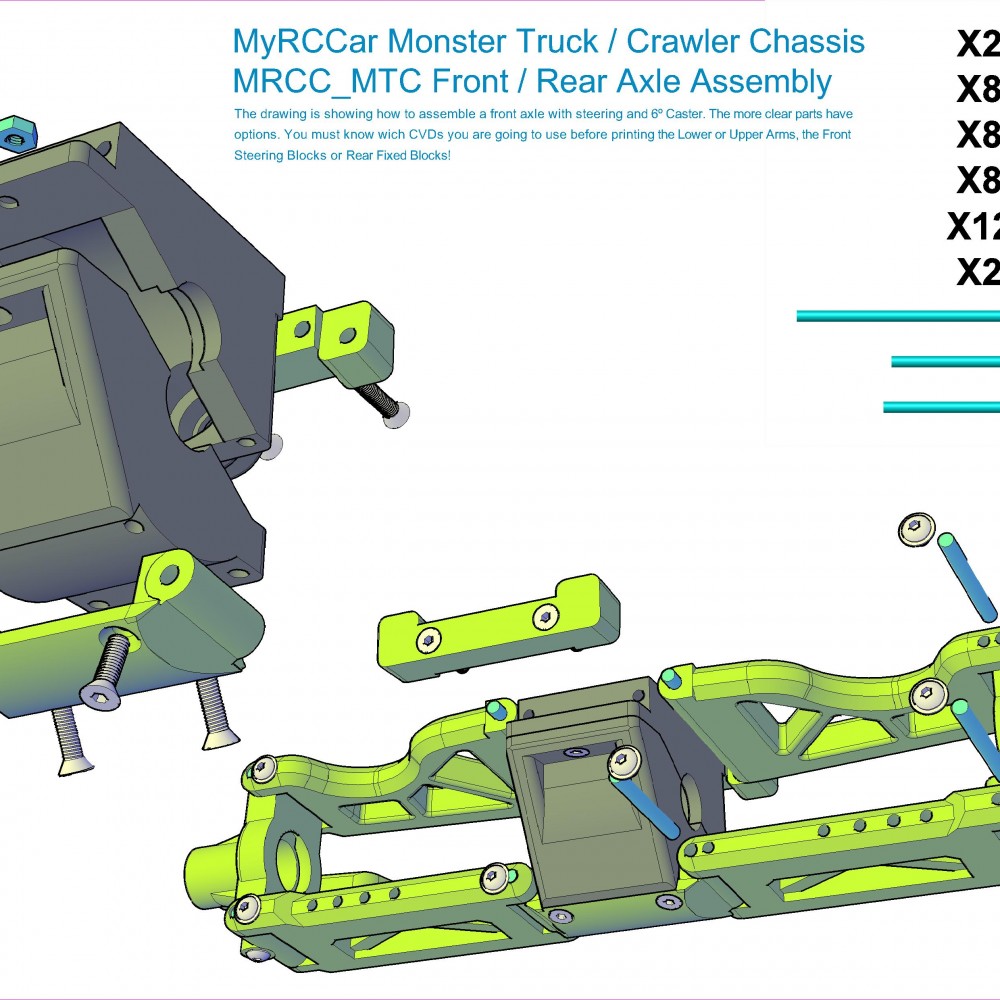
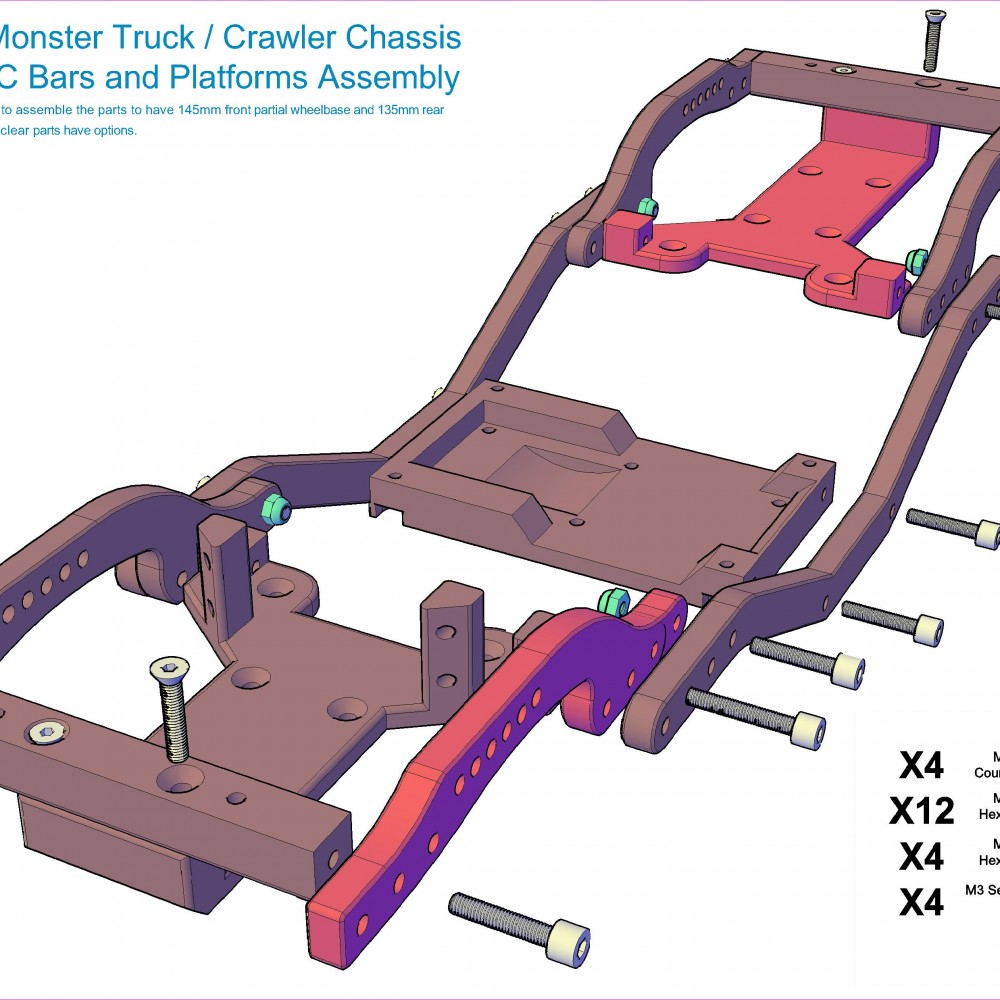
After finishing with the OBTS chassis I knew I was not covering all RC car types with that one. That's why the MTC chassis started to appear in my mind.I finally activated my PayPal account, so please, feel free to tip me if you want to help :) Old Price: 13.62 The main goal this time is to have a great clearance, so the center of gravity is also higher. This will make the car to roll over if you turn close at high speeds. Also all the parts are a little over-sized to be as strong as possible, but maybe this makes the car a little heavy too. The way I designed this chassis can be observed in the evolution of my publications in thingiverse. I had all the ideas finally made real in my mind from the beginning, but I could not face their design challenges all together. That's why my "designing style" for this chassis was something like "let some doors opened" to continue the work in other directions after taking some key design decisions in some points. There are a few successful makes of this chassis now and I also had the chance to test it, improve it and film it! Please, take a look to some of the next videos to know more about this chassis, mostly in the Independent Suspension Version. Here they are: Speed Build Test Drive of the MTC Chassis Yuran Liu's MTC Chassis Video MyRCCar MTC Chassis with the Typical Pickup Body and 1:3 gearbox reduction MTC Chassis with Typical Pickup Body in high-lift mode MTC Chassis with FJ Cruiser Body having fun more than crawling Remember to subscribe to my Youtube Channel if you want to watch my latest videos! This would be the most representative video: CHARACTERISTICS AND OPTIONS The main chassis structure Instead of one big lower plate as in the OBTS chassis, this one is made of "bars" and "platforms". The main measures for the chassis are similar to the ones of an Axial SCX10 and allow you to build a model with a wheelbase from 270 to 330 mm. The shape of the chassis tries to be narrow to fit where an Axial SCX10 would fit. The Axles The MTC chassis design started having just a few options but ended with some more. The most important option is the kind of axles you want to use. I call them like this: Independent Suspension System Version: This version is the first one, and I re-used many already designed parts from OBTS chassis, as the F/R differential housings or the center differential housing. I wanted you to be able to dis-assemble your OBTS chassis and be able to build another kind of chassis with the same sourced parts and a few new printed parts. As I had this parts designed I centred my efforts in designing a chassis which could use them but the same time "let those doors opened" to be able to design and use other parts to make the chassis more versatile. Rigid Axles Version: The RC crawling world is really big and I was not covering their needs with this chassis and it was one of my goals. Trying to use the same sourced parts than in the other version of MTC or OBTS chassis I designed a compatible system for Rigid Axles of various widths and a multilink suspension system for them which should allow the use of different wheelbases too. But this kind of chassis needs a special kind of central transmission. I designed what I call a "Double Cardan Variable Length Transmission" as this part is not as easy to source as the others. The fun thing is that, as they share the main part of the chassis and center differential, you can also build an Hybrid! I mean a car with front independent suspension system and a Rigid Axle in the rear. Obviously you could also build the inverse hybrid but I think it is not common. The Gearbox This chassis can use the same Center Differential Housing than OBTS one, mounted over the central platform. This is how I started doing my first tests with this chassis. This can be enough if you don't have big wheels and have the right motor + ESC. This was not my case. I bought 128mm diameter wheels and had the motors from my previous "speedy" OBTS builds. So... my motor got really hot very quick, that's when I realised I needed to "gear up" the thing. So I designed a new Gearbox which can be mounted in the same place than the simple center diff. housing and will allow you to choose between various reduction ratios :) And the best of all is you can use it also as simple center diff. just introducing the differential into its housing in the reversed position, in which the motor pinion attacks directly to the differential main gear. The gearbox is heavier, use 4 extra bearings and the access to motor mount screws is harder but I think it really worth it! Steering in both axles If you are thinking in building a kind of Monster or Crawler with steering in both axles, you are lucky! The symmetry in front / rear part of this chassis will allow you to do it. The only thing is that you will need to put your battery higher, over the "Top-Cover" parts. For the rest of these building instructions, we are going to take the Independent Suspension System Version with gearbox. That means all things related to the Rigid Axles, Multilink Suspension System and the Double Cardan Variable Length Transmission will be shared and explained in another publication. This way I can re-use and try to improve and resume my previously made instructions. Options, but not so much This chassis should allow you to build a Monster Truck, Crawler or Scale RC car. The transmission system is the same than in OBTS chassis but you can use a reduction gearbox with differential instead of the simple central differential. The main option for this Independent Suspension System Version is THE WHEELBASE. The parts of the chassis will allow you to build a model with a wheelbase from 270 to 310 mm just moving the front and rear platforms. If this is your case, align all four holes from the center side bar and the F/R side bar. If you want the extra 10 or 20 mm to build a 320 or 330 mm wheelbase model you will also have to displace Front and/or Rear side bars those extra 10 mm so just 3 of the holes will be aligned. But which wheelbase should I use? If you have in mind to build a Scale car you will want it to have the same wheelbase than your real car model. With this chassis the exact available wheelbases are 270, 280, 290, 300, 310, 320 and 330 mm. If you want to use the [FJ Cruiser Body] or the [Typical Pickup Body] you must build a 270 or 280 mm wheelbase for the FJ Cruiser and a 290 mm wheelbase chassis for the Pickup. I recently published a longer bed for the pickup to make 310 mm wheelbase version. And now that you know your main wheelbase you must know which front partial wheelbase and rear partial wheelbase you want. If you plan to use big motors (longer than 50mm) you will need 145 mm front partial wheelbase or bigger, 135 mm version won't be enough. Also, if you use same partial wheelbase in the front and the rear, you will be able to use same length central dogbones. If you don't want to "re-design" the adaptors for the FJ Cruiser use 145mm front partial wheelbase and 135mm rear wheelbase for, is also the combination I will use as an example.If you want to use the 290 Pickup Body use 145+145mm partial wheelbases, and 155+155 for the 310mm version REQUIRED ELECTRONICS AND COMMON SOURCED PARTS I'm going to re-use here the info from my previous publication for OBTS chassis. Why?¿? Am I so lazy?¿? Maybe, but the reason is I designed this chassis to use the same parts than the OBTS one, so mostly same parts are needed. [In the OBTS Chassis publication] you will find many more info about how to source parts, the range of prices, how much can you spend on sourced parts depending of your choices... This time I'm going to do it a little different... I'm going to list and link to sourced parts I have used, bought as part of a kit or as spares. There we gooo! All MyRCCar projects are around the same sourced parts. We could consider they are common 1/10 parts and you can source them from different brands and shops. This list could be helpful for you to consider every little thing you have to buy, how many orders to how many shops you have to do, the shipping costs etc. As I live in Spain, I will choose some shops convenient for me. I hope some of you can share other lists with other shops more convenient for other zones of the planet :) Hey! Many examples here, but you won't need all of this things to make a MyRCCar. Think carefully if you need each of them. Electronic Parts 2CH or 3CH Radio + Receiver [HK 2CH example] ; [HK 3CH example] ESC Electronic Speed Controller [HK Brushed example] ; [HK Brushless example] Motor Brushed / Brushless 3650 or bigger for 1/10 [HK Brushed example] ; [HK Brushless example] Servo 5-15KG [HK ~10KG example] ; [HK cheaper one] 2S LiPo Battery [HK small 2.2Ah example] ; [HK big example] LiPo Charger [HK good charger] Lights [HK cheap example] ; [HK very cheap example] Battery/ESC adaptor [HK example XT60] ; [other HK adaptor] Motor/ESC connectors [HK gold connectors] Motor Dissipator with fan [HK big one example] Thermo shrink tube [HK example] Double Side Tape [HK example] Now other "mechanical" parts Shocks and shock oil [HK oil example] [HK vandal shocks example] ; [HK shorter shocks] Wheels and tyres [HK 100mm crawler example] ; [HK monster example] Trooper or STT09304 like Center Diff [HK trooper example] Motor Pinion M1 14-21T [HK cheap 3.17mm hole Mod1 14T example] 2x Front / Rear Diff HSP 02024 or similar [HK vandal example] 2x Front / Rear Pinion HSP 02030 or similar [HK FR pinion example] 2x 1/10 universal cup / vase [HK cheap example] 6x 4.7mm ball-joints with M3 screw [HK example] 20x bearings for wheels, FR diffs and steering [HK cheap 5x10x4 example] ; [HK cheap 10x15x4 example] 4x CVDs from HSP, Vandal or Reely [HK On-road CVD example] ; [HK Off-Road Vandal example] 2x central 1/10 dogbones (Sorry, bought them in local store) 4x 12mm Wheel HEX and pins [HK aluminium example] 4x Typical Clips for battery/shell Holders [HK medium size example] A lot of M3 Screws and 4x M4 self-locking Nuts [HK countersunk example] ; [HK button head example] ; [HK socket head example] ; [HK screw grub example] 3mm piano wire [HK example] O-Ring for MyRCCar Shocks [HK cheap example] Bearing Fitting/Removal Tool [HK example] Velcro Strap [HK example] Car in kit to make OBTS buggy/truggy or MTC chassis [HK Quanum Vandal Kit] ; [HK Vandal ARR version] I bought most of this things, not all, in different orders, which usually needed 7 days to reach my house from the EU warehouse for 0€ shipping costs. LET'S START BUILDING! I tryed to minimize the need to re-print parts when making configuration changes, but it is not possible 100%. Let's start printing some parts that will not change. Bars and platforms: Printing With these parts you will build the main structure for the chassis. It consists on 2 side bars (formed by 3 parts) and 3 platforms, the Front one, with its support for the servo, the Rear one, which have options to maximize battery size available space, and the Central platform. Print1: You can print two [MRCCMTCCentralSideBar]They are swappable, so no need to mirror them. Print2: Print four [MRCCMTCFrontRearSideBar]If you mirror two of them, you will be able to have the same surface finish for all of them when assembled. If this doesn't mind you, they are swappable too. If you plan to use the motor dissipator+fan upgrade you will need some little extra space, maybe you need to print one [MRCCMTCFrontSideBarSHORTER] to replace the front left one. Print3: Time to print the [MRCCMTCPlatformCentral]With this one you will be able to use the gearbox or the simple central differential housing. Print4: Print [MRCCMTCPlatformFront]It has no versions so just print it. If you need some extra distance for your servo as it happened to me, you can use the spacers I attach. Print5: Now you could print [MRCCMTCPlatformRear]You will be able to move this platform to have different rear partial wheelbases, but if you want the maximum space for the battery you will need to print [MRCCMTCPlatformRearPLUS10] for a 145mm rear partial wheelbase or [MRCCMTCPlatformRearPLUS20] for a 135mm rear partial wheelbase. Print6: Print two [MRCCMTCPlatformHolder]These are all the needed parts to do the first assembly! Bars and platforms: Assembling The next drawing shows how to assemble the previous printed parts to get a chassis with 145mm partial front wheelbase and 135mm partial rear wheelbase. The more colourful parts are the ones with options, so pay special attention to them when selecting the ones you need. You can see in the left bottom corner of the drawing that I’m using the middle hole of the 3 in the front of the chassis side bars. That one would be for the 145mm partial front wheelbase while the others are for 135mm and 155mm partial front wheelbases. Use the drawing as a guide to know which screws use and where, but you will need to use them in the right holes for your build. DRAWING1 Now that you have this in your hands you can start feeling the size of your truck! Remember to test if you are printing things "the right size". I would pay special attention to the size of the holes, they are two kind, "passing" and "screwable". Your M3 screws should pass quite easy through "passing" holes. The same way be sure they make a good connection when you screw up one quite strong :S (be careful about how much strong :S). If you are happy with the results, you are ready for the next step!!! Front/Rear Axles: Printing There are just few parts this time that has no options... I mean, you must know which CVDs you want to use in your build to be able to select the proper parts to build your F/R axles. Print7: Print one [MRCCMTCFRDBOTTOM5104]You will have to add supports in your slicing program to print this correctly.The F/R housings are the same than in OBTS chassis, and they are designed to house a HSP 02024 differential and pinion or similar ones. They use two 10x15x4 bearings to hold each diff. and two 5x10x4 bearings to hold each pinion. Remember you will also need two 1/10 standard vases for the diff pinions. Test the bearings, the pinion and the 02024 differential to see if everything is printing fine. If it is, print another one for the other axle. Print8: Print one [MRCCMTCFRDTOP]Hold it with the bottom part and test it with the rest of the sourced parts. If everything looks ok, print the other one for the other axle ;) Print9: Print one [MRCCMTCFRDUAS6C] and one [MRCCMTCFRDUAS0C]Print them if you want 6º Caster in front axle and 0º Caster in the rear axle. This is the caster combination I chose, but you should be able to use 0º or 6º in any of them. Print10: Print one [MRCCMTCFRDLAHolder6c] and one [MRCCMTCFRDLAHolder0c]Print them if you use my caster combination. Choose the right ones for yours. I recommend printing these parts in the provided position adding some easy supports in your slicer. Print11: Print two [MRCCMTCFRDC-HUBFront]These parts are needed to have steering in the front axle and they have no options, but the rest of the parts to print depend of the CVDs you want to use. The suspension arms, the upper and the lower ones depend of the CVD you want to use. With the 715mm from pin to pin version you can use many CVDs, including HSP 106015, HSP 166015, Quanum Vandal Front CVDs and OpenRC Truggy Reely CVDs. If this is your case:Print12a: Print one [MRCCMTCSUSUpperArm715] and one [MRCCMTCSUSLowerArm715]. With the 769mm from pin to pin version you should be able to use HSP 108015 and HSP 188015 CVDs. If you have some of this ones you will need to:Print12b: Print one [MRCCMTCSUSUpperArm769] and one [MRCCMTCSUSLowerArm769] Remember to print just one of each to be able to do the proper tests with your CVDs before printing the ones for the rest of the arms. Now lets print what i call the Front Steering Blocks and the Rear Fixed Blocks, which are completely dependent of your CVDs so... If you are using a Quanum Vandal as a source you will have 2 front CVDs and 2 rear wheel-cups and dogbones. To use them you will need to:Print13a: Print two [MRCCMTCSUSFSBLOCKTYPEA] and two [MRCCMTCSUSRFIXEDBLOCKForVandalDogbones] If you are using HSP 166015 or HSP 188015 CVDs I think you need to use TypeB parts. So...Print13b: Print two [MRCCMTCSUSFSBLOCKTYPEB] and two [MRCCMTCSUSRFIXEDBLOCKTYPEB] If you are using HSP 106015 or 108015 as your CVDs you will need to use TypeC parts. So...Print13c: Print two [MRCCMTCSUSFSBLOCKTYPEC] and two [MRCCMTCSUSRFIXEDBLOCKTYPEC] Finally, if you are using Reely CVDs from your "old" OpenRC Truggy use typeD parts. So...Print13d: Print two [MRCCMTCSUSFSBLOCKTYPED] and two [MRCCMTCSUSRFIXEDBLOCKTYPED] These parts use bearings so be sure they get properly in place. TypeA and TypeD use two 5x10x4 bearings for each wheel. TypeB and TypeC use one 5x10x4 and one 10x15x4 bearings for each wheel. Front/Rear Axles: Assembling Let's first assemble the front axle with 6º Caster. If your diff housing upper and lower parts are working good, attach them the 6º Caster Lower Arms Holderand one of the 6º Caster Upper Arm Supports, the one of the inner side. Use the single M3x8mm Countersunk screw and the simple M3 Nut to hold everything together by now.As a second step, you must try the rest of the parts of a front suspension arm, so use the drawing below to figure out how to assemble it. The 3mm piano wire represented by blue cylinders must pass easy enough to enter with some little hits but not very hard ones, so use some 3mm tool to "re-drill" the holes if needed. DRAWING2 In this stage, you must be able to test if the transmission system works well enough, mostly the CVDs, so if everything works as expected you can print the rest of your upper and lower arms:) Gearbox: Printing If you don't know very good how your motor is going to perform with this "plastic beast", print the gearbox. It allows you to mount the differential in the normal direction and use it with the gearings to have a reduction or you can mount it in the other direction and "attack" the differential directly with the motor pinion. Only if you want to reduce weight at maximum and if you are sure you want the simple pinion/diff central transmission, print the simple central diff housing. Print14: Let's print the [MRCCMTCCDGEARBOXBOTTOMV3]The thingiverse user Botyoyo made some corrections because the gearbox was not correctly designed to fit the SST differentials. The version of the gearbox I link here is modified to correct those problems. Some options here one more time, you can use a "Trooper" central differential or an "SST" central differential. Some users are trying using 02024 as central differential making some mods to it. Look for their published parts or read the comments and forums for more info ;) For Trooper Diff:Print15a: Print [MRCCMTCCDADAPTORSTRO] For SST Diff:Print15b: Print [MRCCMTCCDADAPTORSSST] Print16: Print [MRCCMTCCDGEARBOXTOP]It will be also compatible with the simple central differential housing, the same than the adaptors. As for a first try we are going to use the "reduction gearbox" as a simple central diff, those are all the parts we need by now. Gearbox and Front/Rear Axles: Assembling If you have your electronics, your central diff and your pinion for the motor, I'm quite sure you will want to do some tests. First of all, prepare the two M3 screws and washers you are going to use to hold the motor in their places inside gearbox. You can mount the motor and pinion then. For that, insert the pinion inside the gearbox and then put the motor in place while you insert the shaft of the motor in the pinion. This is kind of tricky ;) You must then screw the motor in place using your tool through the holes in front of the motor screw's heads. Leave it a little loose so you can adjust the final position after inserting the differential. For that, put your adapters in your differential and insert the assembly into the gearbox. Now it's time to adjust and screw the motor in its "final" position. This position is also a hard thing to find, because very far and you are not using the full teeth of your gears and you could have problems. So near with no gap and you will have extra heat which could cause problems too... WARNING! This kind of transmission is probably not good for you, it depends of the kind of motor, if you have full metal transmission, big or small wheels, the quality of your build and printed parts... so expect having problems of heat in your motor, maybe in your plastic parts if there is something not adjusted... many things can go wrong so I hope you can be patient to make things work good :) Sooooooo... Now it's time to put all that we printed together!!! You can see it in the next drawing but it is so easy! Use four M3x12 Countersunk screws to mount each axle on the chassis and six M3x20-30mm (from 20mm to 30mm length) Countersunk screws to mount the gearbox. If your central diff with it's adaptors is on place, you can screw the gearbox/central diff. housing TOP with two M3x12 Grub screws. DRAWING3 At this stage, with all printed parts together, the chassis structure is a little weak. You can take advantage of this to get the central dogbones in their places. Maybe you can do the chassis to flex a little so you can put them in their places, then you release your strength to make the chassis come back to normal position. You can of course put them in place holding them in their position before screwing the 4 screws of an axle. Steering and Covers : Printing What I call "covers" in this chassis are not just that, they have a structural function. They will join important parts of the structure in a geometry which will make the whole chassis be more rigid and strong. The steering parts are easy this time because no options. You will need four 6x12x4 bearings for the steering towers. Print17: Print two [MRCCMTCSteeringPivot] and one [MRCCMTCSteeringPlate] Print18: print [MRCCMTCSteeringTower1Servo] and one [MRCCMTCSteeringTower2]The first one will require supports for the servo arm so add them in your slicer. Print19: Print two [MRCCMTCFRDSteeringHolder]This ones are needed to hold the steering system in place but are also part of the bottom cover of the car, so you will need one also for the rear axle without steering. Print20: Print the two you need from [MRCCMTCCoverBottom135], [MRCCMTCCoverBottom145], [MRCCMTCCoverBottom155] and [MRCCMTCCoverBottom165].Time to choose again! To finish the bottom part of the car we need the bottom covers. This parts are dependent of the partial wheelbases you are using. They can be mounted in the front or the rear for a given partial wheelbase. Print the ones which fit your build. I only used the first two ones by now... Now is time to choose if you want to use motor dissipator with fan or not. If you don't need the extra space for the dissipator and fan for the motor you could...Print21a: Print a normal [MRCCMTCCoverTopCenter] and also a normal [MRCCMTCCoverTopFR] for the front part. If you want to use motor dissipator with fan you will need to...Print21b: Print [MRCCMTCCoverTopCenterCutted] and [MRCCMTCCoverTopFRONT] Print22: Let's also print this upgraded [MRCCMTCCoverTopFRMaxBattSize]Use it for the rear part so you can use big batteries. The thingiverse user Saccco also made a version of this part to get also more space! He and others like Botyoyo or Mario made a great job modifying some parts for their builds and making new ones! Remember to search the web for the latest parts :) If you want your battery to go a little more secure, you can print a battery holder but it depends on your rear partial wheelbase to have the max battery space available for each wheelbase. Print23a: Print one [MRCCMTCBatteryHolder135] if you are using 135mm rear partial wheelbase. Print23b: Print one [MRCCMTCBatteryHolder145] if you are using 145mm rear partial wheelbase. Print23c: Print one [MRCCMTCBatteryHolder155] if you are using 155mm or 165mm rear partial wheelbase. Steering and Covers : Assembling First of all you must insert the 6x12x4 bearings into the towers, then insert the steering pivots in the towers. Is a good moment to screw the ball-joints in the servo arm of the left tower and the steering arms of both towers if you are going to use this ball-joint system. Also attach the steering plate to one of the towers and let it a little loose. Now put the steering parts over the front steering holder and the front bottom cover and use two M3x12mm Countersunk screws to hold them together. Do the same with the rear steering holder and rear bottom cover. Screw them together with two M3x12mm Countersunk screws and two self-locking M3 Nuts. To finally put this bottom parts on the chassis, use eight M3x16 Countersunk screws. The chassis should become quite more rigid after screwing all this bottom parts. DRAWING4 Maybe it's time for you to complete the steering system with the servo link and steering links... You can of course mount the servo on place and make your first steering moves to see if everything is working fine. Remember to screw the steering pivots from the upside, near the servo housing with two M3x10 Countersunk screws. DRAWING5 You are almost there! You only need to mount the top cover, those 4 extra parts over your desktop. Just place the Top cover parts on their final position and screw them with four M3x12mm Countersunk screws for the extreme positions and four M3x16mm Countersunk screws for the central positions. Use the last two drawings as a guide to assemble the parts of this last chapter. And the last thing, place the battery holder. For that, un-screw the two proper screws of the rear axle of the four in the rear platform, put the battery holder in place and screw them again :) Now with this, some double-sided tape and maybe a Velcro strap you can mount all the electronics in the car and make your first try’s!!! LAST BUT IMPORTANT THINGS The Shock Holders Quickly but with quality let's print the shock holders. If you have long (95-105mm) shocks...Print24a: Print [MRCCMTCShockHolderPair6c10mmhigher] and [MRCCMTCShockHolderPair0c10mmhigher]Print these ones if you are using 6º Caster in one axle and 0º in the other, or the ones you need for your build If you have shorter (80-95mm) shocks...Print24b: Print [MRCCMTCShockHolderPair6c] and [MRCCMTCShockHolderPair0c]Print these ones if you are using 6º Caster in one axle and 0º in the other, or the ones you need for your build The shock holders must be mounted in the right position with a M3x12-16 Button-Head screw. Can you figure out which hole will be the right one? If you have long shocks and want more strength...Print24c: Print [MRCCMTCShockHolderPair6cSTRONG] and [MRCCMTCShockHolderPair0cSTRONG]Print this version of the 10mmhigher ones if you are using 6º Caster in one axle and 0º in the other and you want extra strength. They use two M3 screws each; you will probably need 1 long grub screw for the 6º ones Steering Links and Servo Link It's time to finish the installation of the 4.7mm ball-joints with M3 screws in the steering blocks and the servo arm. The links will be composed by two 3d printed ball-joint link extremes and a proper length head-cutted M3 screw or long M3 grub screw. You will need to print the small version of the link extreme for the servo link, and the normal ones for the steering pins (links), so... Print25: Print two [MRCCMTCSteeringBalljointExtremeSmall]They have 7mm depth holes so calculate the length of the screw you need so there is screw inside the most part of the holes when correctly installed. Print26: Print four [MRCCMTCSteeringBalljointExtremeNormal] or [MRCCMTCSteeringBalljointExtremeMedium]Choose the Normal ones if you can so you can have more screw inside extremes holes so the link will be stronger. You will need some extra M3 screws for the steering links, the servo one, the shocks... The central Dogbones About the central dogbones... I just tested the Trooper diff and the SST diff. I use a 80mm from pin to pin dogbone (HSP 06022) for 145mm front partial wheelbase (should be 82mm). Maybe HSP 08059 or 08029 can work for 145PWB but untested! I have also used a 73mm from pin to pin dogbone for 135mm rear partial wheelbase. Maybe something near 91-92mm works for 155 partial wheelbase and 100-101mm for 165mm partial wheelbase but i did not test those. The optional Battery Box If you don't mind about the center of gravity of the chassis or if you want rear steering maybe you can use the Battery Box I created for the Rigid Axles Version. You can use a max size 154x54x20 mm battery, maybe a little higher than 20mm would not matter. Hey :) Now you should have a functional RC Monster, more than crawler because of the actual transmission... give it a try but always reading temperature somehow... in the motor and the nearby! Break and re-print as much plastic parts as you want but take special care of the sourced ones... you are trying to avoid to place an order or have to visit a store with your 3d printed RC car! Print27: You want it?¿? Print [MRCCMTCRigAxlesTopBatteryBox] To assemble it you will need 2 extra M3x10 Counter-Sunk screws for the rear part holes and maybe 2 self-locking nuts. If you can, replace the screws from the central part from countersunk to +2mm longer socket head ones. USING THE REDUCTION GEARBOX If you want less speed and more torque it's time to print some extra gears and assemble them into the gearbox!I originally designed this gearbox as a 1:4 reduction gearbox with a very simple setup: The motor has a 14T pinion which attacks a 28T spur. This is the first 1:2 reduction Previous Spur shares axle with 14T printed pinion which attacks another 28T Spur. This is the second 1:2 reduction Previous Spur shares axle with the 14T pinion which attacks the 44T Center Diff. This is another 1:3.14 reduction The center diff shares axle with F/R diff pinions. They are 13T and attack the F/R diffs which I think are 38T. This makes the final 1:2.92 reduction So what is the total reduction ratio for the transmission?¿? 1/2 X 1/2 X 1/3.14 X 1/2.92Using the Trooper Diff, a 14T motor pinion and the provided gear box the total gearing ratio is aprox. 1:37 Now you can change the external gears to change the reduction ratio. You can achieve aprox. 1:2, 1:3 or 1:4 ratios just changing 2 gears!The working couples are: 15T with 28T for aprox. 1:4 reduction17T with 26T for aprox. 1:3 reduction21T with 22T for aprox. 1:2 reduction There are 3 versions of the pinion which attacks the differential. Use the 13T or 14T for SST 46T differential and the 14T or 15T for the 44T Trooper differential. If you use a 14T motor pinion and also a 14T diff pinion you will be able to "swap" your center differential to use the car without the gearbox reduction. Let's see what you would need to print for this particular case... Print28: For SST diff. print [MRCCMTCCDGEARBOX13TDiffPinion] or [MRCCMTCCDGEARBOX14TDiffPinion] and for Trooper diff. print [MRCCMTCCDGEARBOX14TDiffPinion] or [MRCCMTCCDGEARBOX15TDiffPinion]The other gear you will need to assemble with this pinion is part of the external gears couple Print29: Print the long axle, this [MRCCMTCCDGEARBOXLongAxle] and a 28T gear [MRCCMTCCDGEARBOXMod128Tgear]You will need to assemble the gears over this axle. The one in the side of the motor pinion needs to be 28T for a 14T motor pinion and the other one is part of the external gears couple. Now let's print the external couple of gears: Print30a: For aprox. 1:4 extra reduction print [MRCCMTCCDGEARBOXMod115Tgear] and [MRCCMTCCDGEARBOXMod128TgearwithHoles] Print30b: For aprox. 1:3 extra reduction print [MRCCMTCCDGEARBOXMod117Tgear] and [MRCCMTCCDGEARBOXMod126Tgear] Print30c: For aprox. 1:2 extra reduction print [MRCCMTCCDGEARBOXMod121Tgear] and [MRCCMTCCDGEARBOXMod1_22Tgear] To assemble all... OMG it is kind of a puzzle!!! You will need four 10x15x4 bearings and three M3x8 Button-head screws, maybe some washers.So... the instructions for this are: - Solve the puzzle! Maybe some of you want to make a video of how to assemble it and finish now and forever with the mystery ;) Just a big clue: Start introducing the bearings, then the "diffPinion"-> the inside gear->the long axle->... ------- Have fun and remember to share your make with us, the same than your experiences with it... let's learn ones from the others! If you find something important missing or some error in this info please tell me and I'll try to correct it as soon as possible :) I hope you enjoy reading or building this chassis! See you in MyRCCar Group?¿?
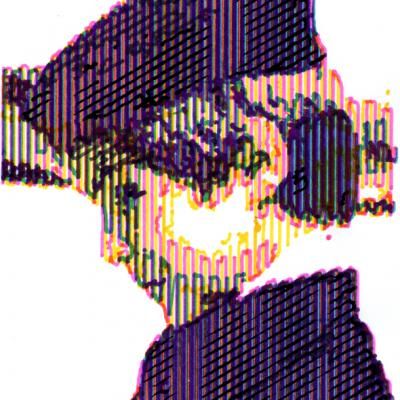